Paper
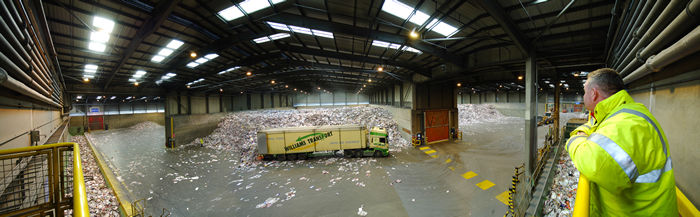
Paper and magazine collected at bring sites arrive at Aylesford Newsprint and are checked for quality as the load is tipped into one of the four bays each with a capacity of 2,500 tonnes. The batch is fed onto conveyor belts and enters two large rotating drums where it is mixed with water to swell and separate the fibres to become a pulp, Screening separates the fibres and water from large contaminates such as cans, plastic bottles and free magazine gifts, which are ejected onto a conveyor belt for disposal.
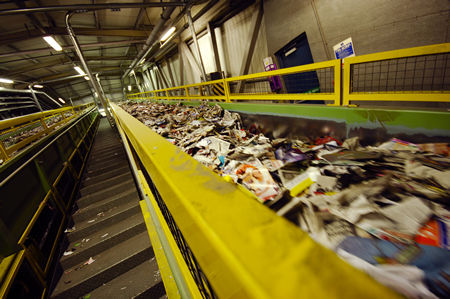
The fibre and water mixture (pulp) is then put through a series of cyclone screens, which remove smaller items such as plastics and staples.
Compressed air is used to form soap bubbles to remove the ink from the mixture. The ink sticks to the bubbles as they float to the surface forming a scum that can be removed mechanically. The pulp then goes through further cleaning stages before hydrogen peroxide is added to brighten the fibres then it is laid on a “forming sheet” and fed through the machine.
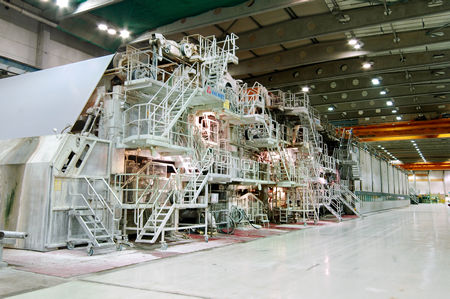
This removes the water from the pulp and dries it, the newly made paper is wound onto reels and transported to publishers throughout the UK, Europe and some further a field. They recycle 500,000 tonnes, about one in seven newspapers and magazines every year. This advanced process means papers can be recycled up to 8 times before the fibres become too short to knit back together again. It takes 10 days for yesterday’s newspapers to reappear on newsstands across the UK and Europe. The only thing to change will be the stories.
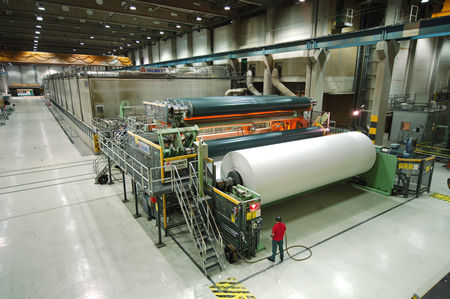
